In den Aufbau digitaler Fabriken investieren Unternehmen weltweit jedes Jahr mehr als eine Billion Euro. Mehr als die Hälfte der 700 befragten Unternehmen sind allerdings noch in einem sehr frühen Stadium der Implementierung digitaler Systeme und Technologien.
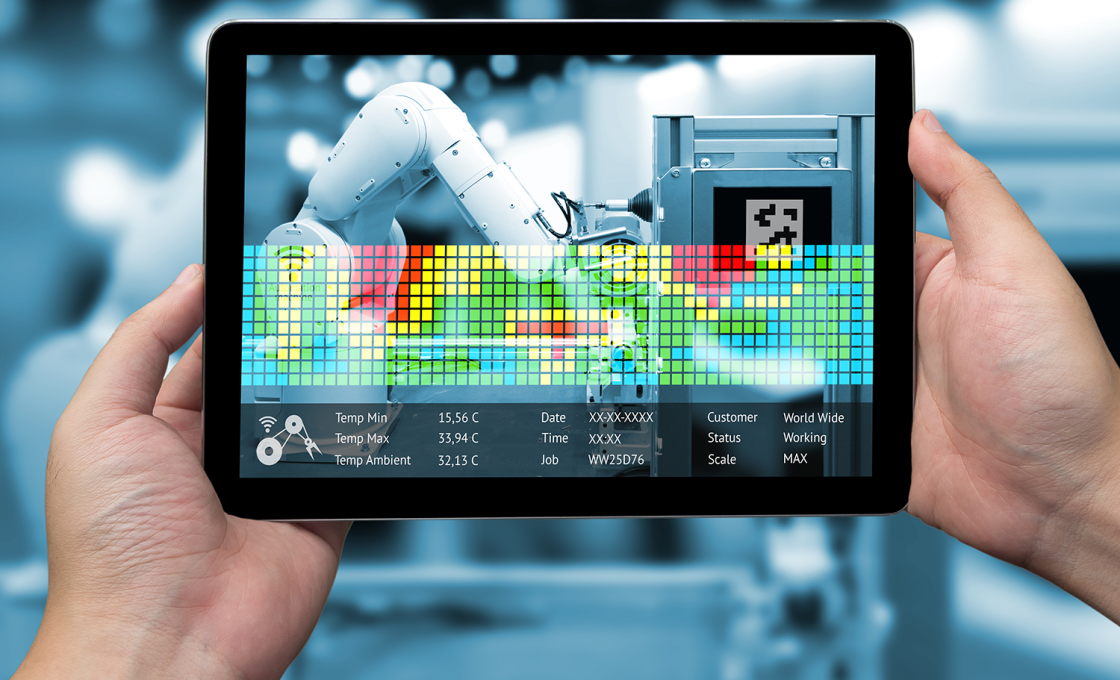
Unternehmen, die mindestens 3 Prozent ihres Nettoumsatzes in ihre digitale Transformation investieren, profitieren häufig von höheren Renditen und einer schnelleren Amortisation. Das geht aus der Digital Factory Transformation Survey 2022 hervor, die die Wirtschaftsprüfungs- und Beratungsgesellschaft PwC Deutschland anlässlich der Hannover Messe veröffentlicht. Die Industrie investiert demnach weltweit jährlich mehr als eine Billion Euro in die digitale Fabrik bzw. Programme zur digitalen Transformation.
Die Pwc Digital Factory Transformation Survey 2022 wurde im zweiten Halbjahr 2021 durchgeführt. Befragt wurden weltweit 700 Unternehmen aus 23 Ländern, darunter 100 mit Hauptsitz in Deutschland. Abhängig von der Reife im Hinblick auf die Transformation zur digitalen Fabrik und vom Umfang der IT-Implementierung, ordnet die Studie die befragten Unternehmen in vier Kategorien ein: Als Digital Champions gelten die 10 Prozent der am höchsten bewerteten Unternehmen, die ihre Digitalisierung ganz oder zum größten Teil abgeschlossen haben. Die nächstfolgende Gruppe sind mit 20 Prozent die Innovators, die in ihrer Transformation große Fortschritte erzielt haben. Die Gruppe der Follower umfasst 40 Prozent. Diese Unternehmen haben einen Fahrplan für die Digitalisierung erstellt und befinden sich in einer frühen Stufe der Umsetzung. Als Novices gelten Unternehmen, die gerade mit der Planung der Digitalisierung begonnen haben. Diese Gruppe umfasst 19 Prozent.
Flexibilität und Resilienz statt Kostensenkung in der digitalen Fabrik
Die vergangenen Jahre waren für produzierende Unternehmen von anhaltenden Krisen geprägt: Unterbrochene Lieferketten, große Nachfrageschwankungen und der akute Inflationsdruck sind nur einige der Herausforderungen, denen sich die Betriebe bis heute stellen müssen. Infolgedessen waren fast alle Unternehmen gezwungen, ihre Produktion flexibler zu gestalten und auf ein Wertschöpfungskettenmodell zu setzen, das Resilienz in den Fokus rückt.
Wo früher Kostensenkung und Effizienz im Vordergrund standen, rücken heute Flexibilität und Resilienz in den Vordergrund. Viele Unternehmen investieren deshalb in ihre digitale Transformation. Die globale Befragung von 700 Industrieunternehmen zeigt, dass die Zahl der Unternehmen, die digitale Technologien zur Senkung von Kosten einsetzen, drastisch eingebrochen ist, während die Zahl der Unternehmen, die investieren, um ihre Flexibilität und Resilienz zu stärken, insgesamt um 76 Prozent gestiegen ist.
Auch der wachsende Stellenwert von nachhaltigen Produktionsabläufen hat die Art und Weise, wie Unternehmen in die Zukunft investieren, stark verändert. Die Befürchtung, dass die Corona-Krise das Thema Nachhaltigkeit bei den großen Industrieunternehmen in den Hintergrund drängen würde, hat sich als falsch herausgestellt. Das Gegenteil ist der Fall: Die Zahl der Unternehmen, die in digitale Technologien investieren, um nachhaltiger zu wirtschaften, hat sich mehr als verdoppelt. „Die Studie zeigt, dass die Investitionen in Nachhaltigkeit schon aufgrund der zunehmenden regulatorischen Anforderungen stark vorangetrieben wurden“, erklärt Dr. Reinhard Geissbauer, Partner und Head of Digital Transformation Europe bei PwC Deutschland. „Der Bedarf nach operativer Resilienz hat diese Dynamik zusätzlich erhöht.“
ERP, Fertigungssteuerung und das Internet der Dinge
Die neue PwC-Studie zeigt, dass die digitale Transformation in der Industrie viele Facetten hat: Unternehmen setzen auf „Backbone“-IT-Systeme wie die weit verbreiteten Systeme für Enterprise Resource-Planning (ERP) und Manufacturing Execution Systeme (MES), aber auch auf neue Innovationen wie Betriebsplattformen für Geräte und Sensoren, die über das Industrial Internet of Things vernetzt sind. Darüber hinaus finden sich in vielen Betrieben softwarebasierte Business Anwendungen oder Use Cases wie Systeme zur Steuerung der Produktionsqualität oder zur Wartung von Maschinen. Zudem sind vielerorts Technologien wie Drohnen, Wearables oder automatisierte Roboterfahrzeuge im Einsatz. „Produktionsunternehmen erkennen jetzt, dass viele dieser digitalen Innovationen kombiniert werden müssen, um Fertigungsprozesse zu transformieren – vom Design bis zum Vertrieb“, berichtet Michael Bruns, Partner bei PwC Deutschland.
Digitalisierungstempo trifft nicht die Erwartungen
Die Studie zeigt auch: Trotz der Fülle an neuen Technologien und der hohen Investitionen können viele Unternehmen ihre Digitalisierungspläne nicht umsetzen. Für die Unternehmen ist es häufig schwieriger als erwartet, die Digitalisierung konsequent voranzutreiben. Zur Einordnung: In einer PwC-Umfrage aus dem Jahr 2014 hatten 80 Prozent der Unternehmen angegeben, dass sie ihre Digitalisierungsprojekte bis Ende 2019 abschließen wollen. Diese optimistischen Erwartungen wurden vielerorts enttäuscht.
Obwohl die Implementierungsrate neuer IT-Systeme, digitaler Geschäftsanwendungen und angewandter Technologien in den vergangenen vier Jahren stark anstiegt, ist der digitale Reifegrad bei vielen der weltweit größten Industrieunternehmen immer noch nicht da, wo er sein sollte. Mehr als 60 Prozent der Unternehmen befinden sich noch in der Anfangsphase ihrer digitalen Transformation. Lediglich 10 Prozent profitieren bereits von den hohen Erträgen, der Flexibilität und der Resilienz ihrer vollständig abgeschlossenen, digitalen Transformation oder sind zumindest kurz davor.
Digitales Rückgrat als Erfolgsfaktor
Die Experten von PwC haben im Rahmen der Untersuchung vier Erfolgsfaktoren identifiziert, welche die Digital Champions auszeichnen. Die Studienergebnisse zeigen, dass diese Unternehmen die richtige digitale Strategie entwickelt und sich auf die relevantesten Technologien konzentriert haben. Außerdem haben sie ein standardisiertes, digitales Rückgrat aus unterstützenden IT-Systemen entwickelt und ihre Organisationsstruktur so angepasst, dass sie digitale Betriebsmodelle aktiv trägt.
„Organisatorische Unterstützung und verbesserte Fähigkeiten sind für den Erfolg von Digitalisierungsprogrammen entscheidend – ohne sie kann die sich die transformative Kraft digitaler Technologien nicht im Unternehmen entfalten“, erklärt Geissbauer. Unternehmen müssten zudem erhebliche Investitionen in die Konnektivität und in die Harmonisierung ihrer Systeme tätigen, um in verschiedenen Betriebsumgebungen neue Arbeitsweisen einzuführen.
Höhere Investitionen führen zu höheren Renditen
Die Unternehmen aus der PwC-Umfrage planen in den kommenden Jahren Investitionen in Höhe von 1,8 Prozent ihres Jahresnettoumsatzes. Im Vergleich zu früheren PwC-Studien ist das ein deutlicher Anstieg. Dies entspricht einem geschätzten Gesamtvolumen für digitale Investitionen in der verarbeitenden Industrie von mehr als einer Billionen Euro. Dennoch sollten laut PwC einige Unternehmen ihre Investitionsraten weiter erhöhen, da die Studie eine starke Korrelation zwischen hohen Investitionen und hohen Renditen aufzeigt. Laut Studie liegt die Wahrscheinlichkeit für höhere Erträge bei Unternehmen, die mehr als 3 Prozent ihres jährlichen Nettoumsatzes in die digitale Transformation ihrer Fabriken investieren, 2,5-mal höher als bei Unternehmen, die weniger als 2 Prozent investieren.
Aus der Studie geht zudem hervor, dass Unternehmen, die größere Investitionen in die Digitalisierung tätigen und das damit einhergehende Risiko in Kauf nehmen, oft bessere Ergebnisse erzielen und ihre Investitionen schneller amortisieren. Die meisten Investitionen in digitale Technologien haben eine Amortisationszeit von etwa drei Jahren, aber in einigen Fällen können sich selbst umfangreiche Investitionen in grundlegende Technologien wie IT-Backbone-Systeme innerhalb eines Jahres amortisieren.
Transformation kennt kein allgemeingültiges Rezept
„Es gibt keine allgemeingültige Formel für die digitale Transformation“, erläutert Michael Bruns. „Der Projekterfolg stellt sich nur in einem komplexen Zusammenspiel von systemischen Veränderungen der IT-Architektur, der Ausarbeitung von Business Use Cases und der Implementierung spezifischer Technologien ein. Wer zu wenig investiert, verpasst transformative Technologien. Im Umkehrschluss kann aber auch zu viel in Anwendungen investiert werden, die für das Geschäft nicht relevant sind.“
Insgesamt zeigt die Studie, dass Unternehmen, die auf eine wohlüberlegte Auswahl von Technologien und Anwendungsfällen setzen und das richtige Gleichgewicht zwischen standardisierten Systemen und Flexibilität bei lokalen Rollouts finden, am ehesten überdurchschnittliche Erträge aus der digitalen Transformation erzielen. Jürgen Frisch