Digitale Zwillinge sind für die Industrie 4.0 essentiell. Ihre Implementierung setzt jedoch eine sorgfältige Planung und Ausführung voraus. Damit dies reibungslos funktioniert, sollten Industrieunternehmen strukturiert vorgehen.
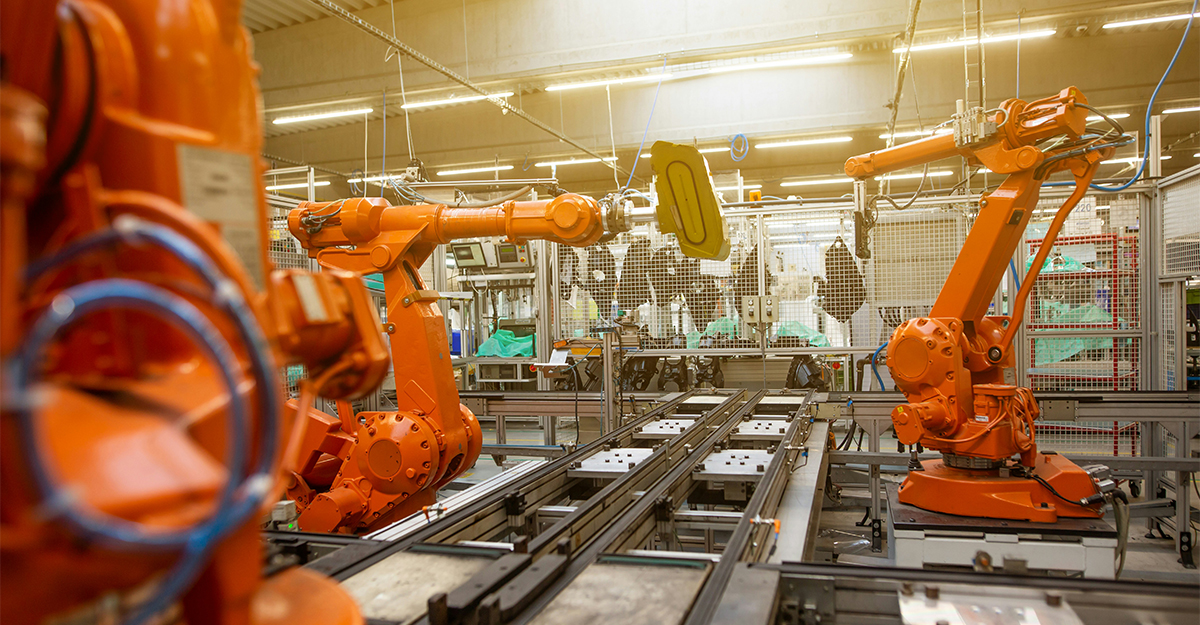
Viele produzierende Betriebe haben in den vergangenen Jahren in ihre Digitalisierung investiert – schließlich stehen sie unter enormen Druck, Prozesse effizienter zu gestalten und die erforderliche Produktqualität trotz fehlender Ressourcen zu gewährleisten. So wurden neue Sensoren eingeführt, um Bauteile zu tracken oder Produktionsanlagen zu überwachen. Wenn es allerdings darum geht, das komplexe Geflecht in einer Fertigung wirklich zu verstehen und zu optimieren, sind Digitale Zwillinge hilfreich. Damit Realisierung, Implementierung und Betrieb reibungslos funktionieren, sollte sich die Industrie Schritt für Schritt an die Umsetzung machen, so eine Empfehlung von NTT Data, ein Unternehmen für digitale Business- und IT-Dienstleistungen.
Schritt 1: Verständnis des Konzepts
Bevor Unternehmen starten, müssen sie erst einmal die Technologie genau verstehen. Ein Digitaler Zwilling ist eine virtuelle Darstellung eines physischen Produkts oder Prozesses, die mithilfe von Echtzeitdaten dessen Verhalten simuliert und analysiert. In der Fertigung können Digitale Zwillinge beispielsweise eine virtuelle Version einer Maschine, einer Produktionsanlage oder einer kompletten Fabrik sein. Dieses Abbild ermöglicht es den Ingenieuren und Betreibern, verschiedene Szenarien zu simulieren, die Auswirkungen von Änderungen vorherzusagen und die Leistung in Echtzeit zu überwachen. Die Königsdisziplin ist schließlich ein bidirektionales System, bei dem der Digitale Zwilling sein Pendant in der realen Welt nahezu vollständig selbst steuert.
Schritt 2: Identifizierung der Ziele
Als nächstes müssen Unternehmen grundlegende Fragen klären und ein gemeinsames Verständnis über Art und Umfang des Digitalen Zwillings entwickeln. Geht es nur um ein gerendertes, bewegtes 3D-Modell oder um einen realen Anwendungsfall wie die virtuelle Inbetriebnahme einer Produktionslinie? Die Festlegung klarer Ziele – ob nun die Verbesserung der Anlageneffizienz, die Steigerung der Produktqualität, die Reduzierung von Ausfallzeiten oder die Optimierung der Ausbildungs- und Wartungsprozesse – hilft dabei, den Fokus während des Implementierungsprozesses zu behalten und sicherzustellen, dass die Investition in den Digitalen Zwilling einen messbaren Mehrwert für das Unternehmen bietet.
Schritt 3: Auswahl der richtigen Technologie
Ein Digitaler Zwilling umfasst zunächst einmal eine Kombination aus Sensoren, Datenbanken, Algorithmen und Visualisierungswerkzeugen, die die zu erfassenden Informationen strukturieren (ontologisches Modell). Sensoren sammeln Informationen aus der physischen Umgebung, welche dann in Datenbanken gespeichert und verarbeitet werden. Mithilfe von Algorithmen werden diese Daten analysiert und in ein virtuelles Modell umgewandelt. Visualisierungswerkzeuge wiederum helfen, den Digitalen Zwilling zu betrachten und detailliert zu analysieren. Gleichzeitig ist der Digitale Zwilling eng mit Technologien wie Edge Computing und Private 5G verbunden. Die Datenverarbeitung direkt vor Ort verhindert Verzögerungen, die bei der Übertragung in ein zentrales Rechenzentrum oder die Cloud unweigerlich entstehen. In der Produktionsumgebung selbst sorgt der aktuelle Mobilfunkstandard mit seiner großen Bandbreite und ultraniedrigen Latenz für verzögerungsfreie Übertragungen. So kommen die Daten nicht nur blitzschnell bei den Digitalen Zwillingen an, sondern deren Erkenntnisse und Anweisungen werden auch umgehend zurückgespielt, sodass die Maschinen nahezu in Echtzeit auf Ereignisse reagieren können.
Anzeige
IT-Matchmaker®.guide Industrie 4.0
Einkaufsführer & Standardreferenz für Industrie-4.0-Software
- Fachbeiträge
- Firmenprofile relevanter Anbieter
- Referenzen aus der Praxis
- Produktübersichten
Download Industrie 4.0 Guide
Schritt 4: Integration von Datenquellen
Die Qualität und Verfügbarkeit der Daten spielt bei der Realisierung eines Digitalen Zwillings eine zentrale Rolle. Zunächst müssen die verschiedenen Informationen, die Sensoren und IoT-Konnektoren erfassen, an zentraler Stelle zusammengeführt werden. Genauso wichtig ist es, dass die gelieferten Betriebs- und Umgebungsdaten aus der realen Welt mit weiteren Informationen aus dem Unternehmen wie Stücklisten, Konstruktionsspezifikationen oder Protokollen von Kundenbeschwerden kombiniert werden. Eine umfassende Datenintegration ist entscheidend, um einen genauen und vollständigen Digitalen Zwilling zu erhalten, der ein realistisches Abbild des physischen Produkts oder Prozesses bietet.
Schritt 5: Digitale Zwillinge – Modellierung
Parallel dazu wird ein Modell des realen Objekts erstellt. Unternehmen sollten einem strukturierten und iterativen Prozess für das Entwerfen, Modellieren, Simulieren, Validieren und Verfeinern ihres Digitalen Zwillings folgen. Damit das Modell alle Erwartungen erfüllt, kann es zudem sinnvoll sein, die unterschiedlichen Stakeholder – von Kunden über Lieferanten bis zu Mitarbeitern – in den Entwicklungs- und Testprozess einzubeziehen. Schließlich muss das virtuelle Abbild mit Echtzeitdaten über Zustand, Leistung, Umgebungseinflüsse oder Verhaltensmuster „gefüttert“ und aktuell gehalten werden.
Schritt 6: Digitale Zwillinge brauchen Kontinuierliche Optimierung
Ein Digitaler Zwilling ist kein statisches Konzept, sondern sollte kontinuierlich optimiert und aktualisiert werden, um mit den sich ändernden Anforderungen und Bedingungen Schritt zu halten. Unternehmen sollten die gewonnenen Erkenntnisse nutzen, um Verbesserungen vorzunehmen und neue Funktionen hinzuzufügen. Dies kann die Feinabstimmung von Modellparametern, die Integration neuer Datenquellen oder die Anpassung von Algorithmen umfassen, um die Genauigkeit und Relevanz des Digitalen Zwillings ständig zu verbessern.
„Richtig geplant und umgesetzt, bringt der Digitale Zwilling eine Vielzahl von Vorteilen. Dazu zählen nicht nur die Minimierung von Fehlern oder die Verbesserung der jeweiligen Produktsicherheit: Die daraus resultierende optimierte Steuerung von Anlagen wirkt sich direkt positiv auf die Profitabilität aus“, erklärt Marcus Giehrl, Practice Director Innovations and Smart Technologies bei NTT Ltd. „Eine schlechte Vorbereitung kann jedoch schnell zum Verhängnis werden. Indem Unternehmen Schritt für Schritt vorgehen, stellen sie sicher, dass die Implementierung reibungslos verläuft und die gewünschten Ergebnisse erzielt werden.“
Der Autor
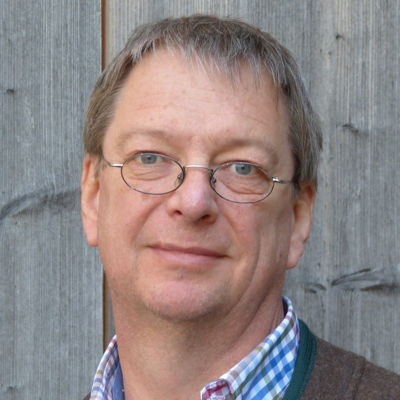
Marcus Giehrl, Practice Director Innovations and Smart Technologies bei NTT Ltd. (ein Unternehmen der NTT DATA, Inc.)