Die Entwicklung neuer Materialien braucht Simulation. Maschinelles Lernen, das selbstständig Wissen erwirbt, soll künftig komplexe Stoffe virtuell entwickeln, prognostizieren Forscher des Karlsruher Instituts für Technologie zusammen mit Kollegen aus Göttingen und Toronto.
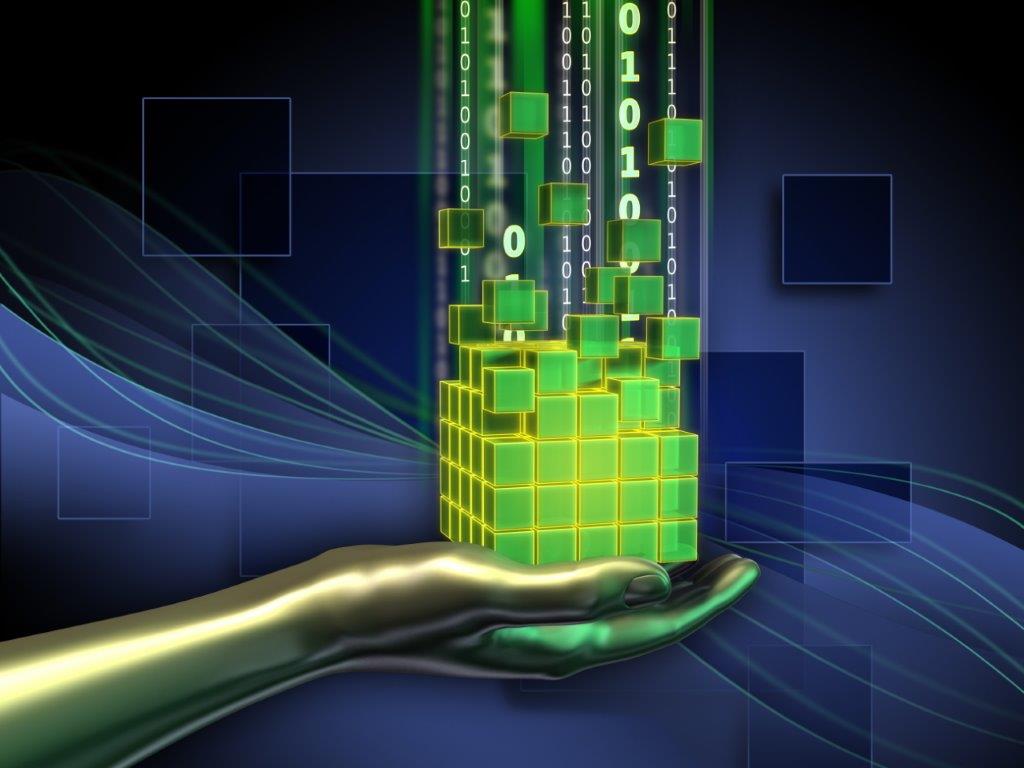
Digitalisierung und Virtualisierung erobern die Materialwissenschaft. Das Erforschen, Entwickeln und Herstellen neuer Materialien hängt entscheidend von schnellen und zugleich genauen Simulationsmethoden ab. Davon wiederum profitieren unterschiedliche Anwendungen – von effizienten Energiespeichern für erneuerbare Energien bis hin zu neuen Medikamenten, deren Entwicklung das Verständnis komplexer biologischer Vorgänge voraussetzt. Künstliche Intelligenz und Maschinellen Lernen können Materialsimulationen entscheidend voranbringen.
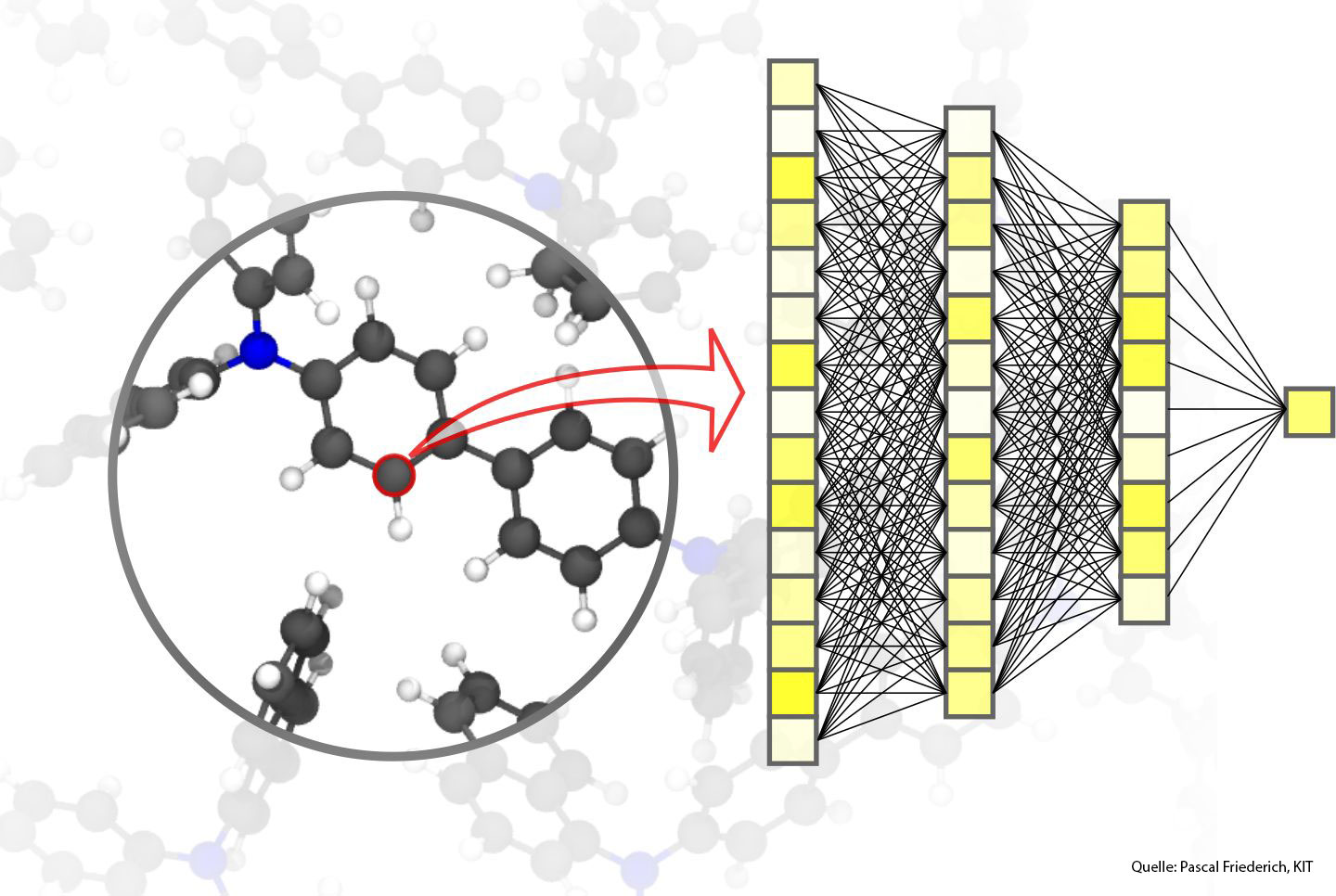
„Gegenüber herkömmlichen Simulationsmethoden, die auf klassischen oder quantenmechanischen Rechnungen basieren, lässt sich mit speziell auf Simulationen zugeschnittenen neuronalen Netzen ein deutlicher Geschwindigkeitsvorteil erreichen“, erklärt der Physiker und Professor Pascal Friederich, Experte für Künstliche Intelligenz und Leiter der Forschungsgruppe AiMat – Artificial Intelligence for Materials Sciences am Institut für Theoretische Informatik (ITI) des KIT. „Schnellere Simulationssysteme werden es in den kommenden Jahren ermöglichen, größere und komplexere Materialsysteme rein virtuell zu entwickeln und sie bis auf die atomare Ebene hinunter zu verstehen und zu optimieren.“
Hohe Präzision vom Atom bis zum Werkstoff
In einem in der Zeitschrift Nature Materials veröffentlichten Artikel gibt Friederich, der auch als assoziierter Gruppenleiter im Bereich Nanomaterials by Information-Guided Design am Institut für Nanotechnologie (INT) des KIT tätig ist, gemeinsam mit Forschern der Universität Göttingen und der University of Toronto einen Überblick über die grundlegenden Prinzipien des für Materialsimulationen eingesetzten Maschinellen Lernens, den Datenerfassungsprozess sowie aktive Lernverfahren. Algorithmen für Maschinelles Lernen ermöglichen Künstlicher Intelligenz, die eingegebenen Daten nicht nur zu verarbeiten, sondern in großen Datensätzen Muster und Korrelationen zu finden, daraus zu lernen und selbstständig Vorhersagen und Entscheidungen zu treffen. Bei Materialsimulationen kommt es darauf an, eine hohe Präzision über verschiedene Zeit- und Größenskalen – vom Atom bis zum Werkstoff – zu erreichen und zugleich die Rechenkosten zu begrenzen. In ihrem Artikel gehen die Wissenschaftler auch auf verschiedene aktuelle Anwendungen ein, wie kleine organische Moleküle und große Biomoleküle, strukturell ungeordnete feste, flüssige und gasförmige Materialien sowie komplexe kristalline Systeme – beispielsweise metallorganische Gerüstverbindungen, die sich zur Gasspeicherung oder zur Stofftrennung, für Sensoren oder für Katalysatoren einsetzen lassen.
Hybride Methoden steigern das Tempo weiter
Um die Möglichkeiten der Materialsimulationen zukünftig noch zu erweitern, schlagen die Forschenden aus Karlsruhe, Göttingen und Toronto vor, hybride Methoden zu entwickeln: Diese verbinden Verfahren des Maschinellen Lernens und der Molekularen Mechanik miteinander. Die letztgenannten Simulationen bedienen sich sogenannter Kraftfelder, um die auf jedes einzelne Teilchen wirkenden Kräfte zu berechnen und damit Bewegungsabläufe vorherzusagen. Die Ähnlichkeit der Potenziale von Machine Learning und Molekularer Mechanik erlaubt eine enge Integration mit variablen Übergangsbereichen. Solche hybriden Methoden könnten künftig beispielsweise die Simulation großer Biomoleküle oder enzymatischer Reaktion noch einmal deutlich beschleunigen. Jürgen Frisch
Anzeige | Fachbeitrag, im IT-Matchmaker®.guide Industrie 4.0 erschienen
![]() |
Artikel
Ansatz zur Umsetzung des Internet of Production in produzierenden Unternehmen |
Autor: | Dr. Michael Riesener, Dr. Christian Dölle & Stefan Perau | WZL der RWTH Aachen University | |
Erschienen: | 2021-03-30 | |
Schlagworte: | Industrie 4.0, Internet of Production, Internet of Things | |
Das Internet of Things(IoT) und die damit einhergehenden Potenziale haben das Umfeld der produzierenden Industrie grundlegend verändert. Damit eine zielgerichtete Aufnahme und Nutzung von Daten innerhalb produzierender Unternehmen ermöglicht wird, wurde das Konzept des Internet of Production (IoP) an der RWTH Aachen entwickelt. Gemeinsam mit und in Unternehmen arbeitet das R&D Intelligence Center der RWTH Aachen an einem ganzheitlichen und systematischen Ansatz, um die Potenziale der Industrie 4.0 im Internet of Production auch für die Entwicklung der produzierenden Unternehmen zugänglich zu machen. | ||
Download |