Der Digitale Zwilling gilt als zentrales Werkzeug für die Industrie 4.0: Eine Fülle möglicher Anwendungsszenarien bietet Fertigungsbetrieben nicht nur Lösungsansätze für Verbesserungen im Produktionsbetrieb, sondern ebnet auch den Weg für neue, digitale Wertschöpfung. Die Asset Administration Shell – kurz AAS oder deutsch digitale Verwaltungsschale – stellt das technische Fundament für ein standardisiertes Datenmanagement im industriellen Einsatz bereit.
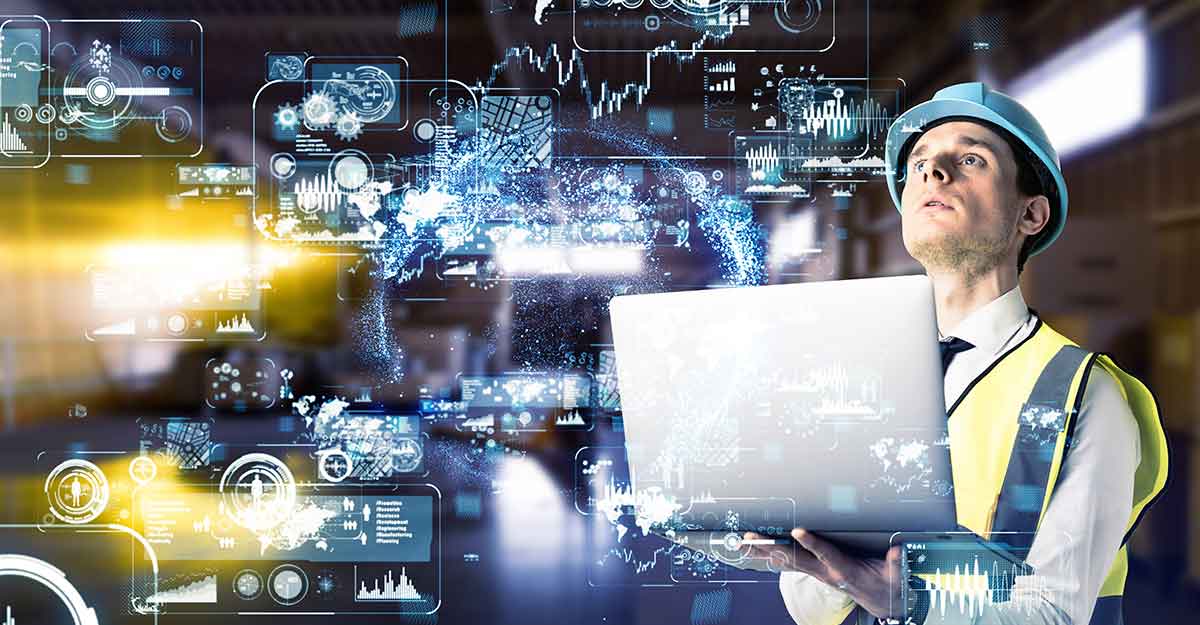
Daten sind für Industrieunternehmen ein wertvoller Rohstoff, den es intelligent einzusetzen gilt, um Optimierungspotenziale zu identifizieren und die Zukunftsfähigkeit zu sichern. Ziel ist die Umsetzung von Industrie 4.0, also das Idealbild einer digital durchgängigen Vernetzung aller in der Fertigung beteiligten Systeme. Um physische Assets wie Maschinen und Anlagen, Werkstücke, Bauteile und Pläne in die digitale Welt der Industrie 4.0 zu integrieren, benötigen Unternehmen virtuelle, dynamische Echtzeit-Modelle, sogenannte Digitale Zwillinge.
Die Herausforderung: Unterschiedlichste Systeme müssen zusammenspielen, heterogene Datenströme bündeln und verarbeiten sowie Informationen mit anderen Digitalen Zwillingen austauschen, je nach Anwendungszweck unternehmensintern oder auch mit externen Akteuren.
AAS als Schlüssel für unternehmensübergreifende Datennutzung
In der Industriebranche geht es dabei zumeist um die Erstellung „digitaler Schatten“ (also ein Abbild von Identität, Zustand und Ort eines Assets) über Unternehmensgrenzen hinweg. Diese Interoperabilität braucht neben einer strategischen IT-Infrastrukturplanung auch standardisierte Formate – umso mehr, je visionärer Fertigungsbetriebe in Richtung dezentraler Daten-Ökosysteme wie Manufacturing-X denken.
Ein Beispiel: Über den Digitalen Produktpass (DPP) werden Hersteller zukünftig sukzessive verpflichtet, CO2-Fußabdrücke ihrer Produkte auszuweisen. Das können sie aber nur, wenn sie aus ihrer Zuliefererkette die relevanten Daten dafür bekommen. Möglich wird dies über die standardisierte Asset Administration Shell (AAS), die durch Standardisierung ein aufwändiges, weil individuelles Bauen von Schnittstellen erübrigt.
Die Verwaltungsschale als standardisierter „Datenstecker“ ist industriereif
Experteninnen und Experten aus Industrieverbänden, Forschung und Politik arbeiten mit Hochdruck an der Etablierung eines solchen herstellerunabhängigen Standards. Ein wichtiger Meilenstein war die Veröffentlichung der Version 3.0 der Asset Administration Shell (AAS) durch die Industrial Digital Twin Association e.V. (IDTA) im Juli 2023: Die praxisreife Spezifikation 3.0 beschreibt, wie Unternehmen diese Verwaltungsschalen aufbereiten und strukturieren, sodass die Daten eines Digitalen Zwillings auf interoperable Weise über den gesamten Lebenszyklus und entlang der Wertschöpfungskette standardisiert zur Verfügung stehen. Jedes Asset kann über seine eigene Verwaltungsschale identifiziert und angesprochen werden und Informationen in einer einheitlichen Sprache bereitstellen. Die Verwaltungsschale fungiert also als standardisierte Schnittstelle für Digitale Zwillinge, vergleichbar mit einem genormten Datenformat.
Anzeige
IT-Matchmaker®.guide Industrie 4.0
Einkaufsführer & Standardreferenz für Industrie-4.0-Software
- Fachbeiträge
- Firmenprofile relevanter Anbieter
- Referenzen aus der Praxis
- Produktübersichten
Zum Download des Industrie-4.0-Guides
Was Digitale Zwillinge in der Fertigungsindustrie bewirken
Von einem standardisierten Datenmodell, durch die Digitale Zwillinge Produktdaten hochgranular auf Einzelstück-Basis nutzbar machen, profitiert die gesamte Wertschöpfungskette. Dies eröffnet eine Vielzahl an Möglichkeiten – ein paar Beispiele:
- Verfeinerte Qualitätsanalysen: Sie erleichtern die Identifikation von Verbesserungspotenzialen in verschiedensten Prozessphasen, von der Entwicklung über die Beschaffung bis hin zur Produktion und Logistik. Im Zusammenspiel mit den Akteuren der gesamten Supply Chain lässt sich außerdem der Aufwand für Rückrufaktionen deutlich senken („Track-and-Trace“).
- Kundenbindung und -begeisterung: Service-Mitarbeitende profitieren von transparenten, detailtiefen Produktnutzungsdaten und können Kund:innen im After Sales individueller beraten und betreuen – für eine höhere Zufriedenheit und Loyalität der Kundschaft.
- Nachhaltige Fertigung: Das standardisierte und automatisierte Sammeln von Produktdaten zum ökologischen Fußabdruck oder zum Energieverbrauch vereinfacht die Umsetzung von Nachhaltigkeitsinitiativen und gesetzlichen Regularien, beispielsweise in Form eines Digitalen Produktpasses.
Von der Effizienzsteigerung zu neuem Wachstum
Über die interne Nutzung der Produktdaten hinaus werden in naher Zukunft dezentrale Daten-Wertschöpfungsmodelle an Bedeutung gewinnen. Der Digitale Zwilling bietet die nötigen infrastrukturellen Voraussetzungen, um die eigenen Daten mit anderen Marktpartnern zu teilen, um somit neue und lukrative Umsatzquellen zu erschließen. Der Grundgedanke einer global vernetzten Datenökonomie ist nicht nur für Konzerne relevant, sondern insbesondere für KMU eine smarte Idee, um Wachstum zu generieren, ohne physisch zu wachsen: Skalierung kann künftig über das Kerngeschäft hinaus durch rein datenbasierte Geschäftsmodelle gelingen. So könnten Maschinenbauer bestimmte Self-Services anbieten, was die Bestellung von Verschleißteilen automatisiert auslöst und den Beschaffungsprozess beschleunigt. Auch ließen sich beispielsweise Szenarien für Geräte- oder Materialwechsel virtuell durchspielen und für eine noch bessere Kundenberatung nutzen. Das steigert den Mehrwert und die Effektivität eines Industrieunternehmens – für einen besseren ROI, zur Abfederung des Fachkräftemangels in der Produktion und für eine risikomindernde Diversifizierung in Krisenzeiten.
Weckruf: Die Potenziale Digitaler Zwillinge zeitnah heben
Der nächste Schritt auf dem Weg zu Industrie 4.0 ist es nun, die technische Steilvorlage der Asset Administration Shell in individuelle Konzepte mit konkreten Mehrwerten zu verwandeln. Die notwendige Sensorik ist in vielen Maschinen bereits vorhanden oder kann im Rahmen eines Retrofits unkompliziert und mit überschaubarem Aufwand nachgerüstet werden. Trotzdem scheuen sich viele Betriebe, die Beobachterposition zu verlassen und eigene Projekte zu initiieren – eine riskante Strategie, denn die deutsche Industrie droht in Sachen Digitalisierung international den Anschluss zu verlieren. Unternehmen können problemlos operativ klein starten, sollten aber von Anfang Themen wie Datenstandards und AAS-Readiness berücksichtigen.
Der Autor
Johannes Fuhrmann, Head of Strategic Business Development Manufacturing bei Arvato Systems.